2023年2月、三菱スペースジェット(旧名称:三菱リージョナルジェット)を開発・製造する三菱航空機株式会社は開発中止を決定しました。2015年11月11日の初飛行から約8年後の大きな決断であり、YS-11以来の国産旅客機の夢は道半ばにて途絶えることになりました。
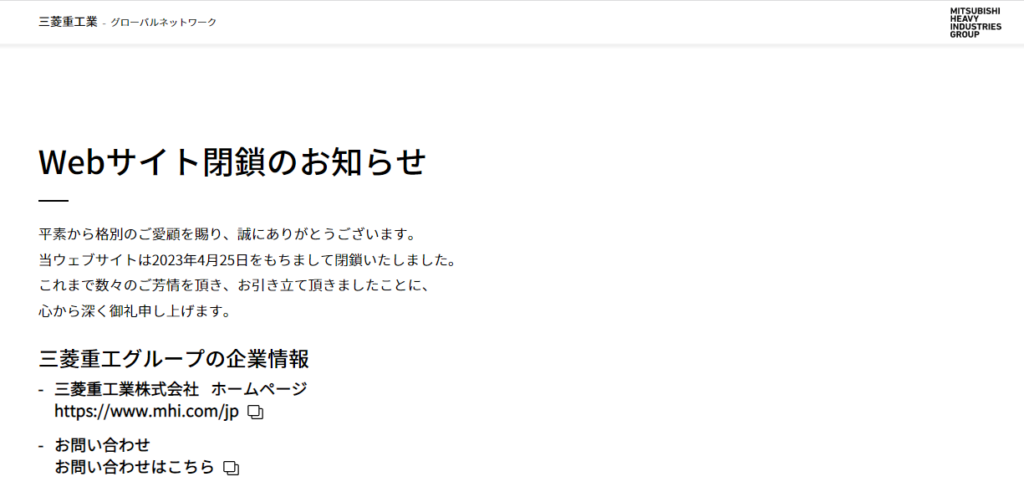
私自身も三菱スペースジェットの就航に大きな期待をしていました。2017年頃の国際航空宇宙展ではモックアップに入場する機会があり、実際に着席して広々とした機内空間に感動したことを覚えています。
今回の記事では、なぜ三菱スペースジェットが機体は完成し初飛行したものの開発中止という決断に至ったのか理由を解説します。
理由は以下の4点です。
①下請けメーカーではなく完成品メーカーとしての経験不足
②社内外での情報交換が出来ていなかったこと
③構築したサプライチェーンが未熟であったこと
④プロジェクトを推進する中心人物が存在しなかったこと
①下請けメーカーではなく完成品メーカーとしての経験不足
三菱重工業は日本の大手重工メーカーとして第二次世界大戦以前より航空機開発に携わっています。自衛隊向けの戦闘機だけではなく、旅客機向けではボーイング787や777などの主要コンポーネントを担当しています。しかし、主要コンポーネントはあくまでも”部品”に過ぎず、完成品メーカーであるボーイングの定めた基準に基づき翼や胴体を設計し、ボーイングのエンジニアの承認を受けて製造され、製造後は再びボーイングのエンジニアの製造検査を受け、米国に所在する生産ラインに載ることになります。この設計~生産のフローから分かる通り、下請けメーカーに与えられた裁量は少なく、問題があればボーイングに相談・報告し、最終判断を仰ぐことになります。
今回の三菱スペースジェットの開発においては、三菱航空機は完成品メーカーとしての立ち位置が求められました。しかし、多くの主席技術者やPMは自分で判断できるほどの経験や責任を持ち合わせておらず、ボーイングのように最終判断する会社や立場の人物不在のまま、プロジェクトが走っていたと想像せざるを得ません。
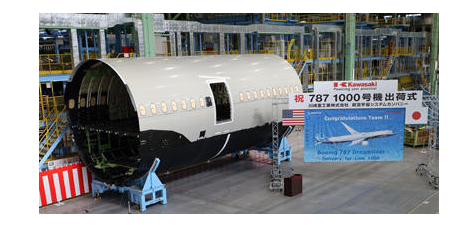
特に、三菱航空機を苦しめたのは品質問題であったと推測されます。ここでの品質というのは、設計図に基づいた製造時点ではなく、この基準に基づいて部品を設計してよいかという設計時点のものです。例えば、上位規格として航空機に使用する材料ではAMS規格(AeroSpace Material Specification)やBMS規格(Boeing Material Specification)、MIL規格(United States Military Standard)が主に採用されています。同様に、航空機製造においては自社規格を設定する必要があり、三菱航空機においても自社規格を設定する際には、「この基準で設計してよいか?」という設計基準を策定時には相当苦労したと推測されます。ボーイングやエアバスなどの長年旅客機製造を行っている完成品メーカーであれば、過去の実績や既存の規格を基に設計すれば良いのですが、新規参入の三菱航空機はこの規格策定から躓いてしまったと推測されます。
②社内外での情報交換が出来ていなかったこと
完成品メーカーとしての経験値が不足している場合、ボーイングやエアバスなどの完成品メーカーからの情報が不可欠となります。しかし、開発の本拠地を日本に設定していたことから、連邦航空局(FAA=Federal Aviation Administration)との連携が不十分であったことは容易に想像ができます。また、本来であれば三菱航空機を指導する立場の国土交通省航空局(JCAB=Japan Civil Aviation Bureau)の経験不足も同様にありました。航空局として認可してよいかの判断が適切にできず、三菱航空機と航空局の間で根拠資料の受け渡しが終わりなく続いていたことも想定されます。このやりとりが議論を行い、結論が出ればよいのですが、判断を行うための資料(=責任を資料提出元の三菱航空機側に持たせる)を要求していたのではないかとも推測されます。
そのため、三菱航空機だけではなく航空局側のノウハウ不足を補うために、社内外での情報交換が必要であったと考えます。
この情報交換が上手くいった事例としては、米国に開発拠点を設置したホンダ エアクラフト カンパニーが挙げられます。
③構築したサプライチェーンが未熟であったこと
仮に設計が順調に進んだ場合であっても、ボーイングやエアバスのように強固なサプライチェーン構築が出来ていなかったため、収益性のあるビジネスとして成り立つ見通しは困難であり、このことも開発中止要因になっていることが考えられます。
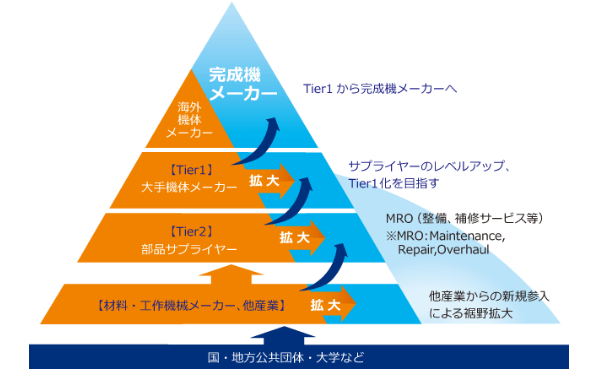
航空機の部品点数は約100万点と言われており、その一つずつに品質だけではなくコスト競争力が必要となります。ものづくりにおいて「ネジ1個の価格は他社製品より数円高いが、1個くらいであれば問題無い」という考えは、後々に悪影響をもたらします。なぜなら、”塵も積もれば山となる”ということわざがあるように、1点ずつの部品が少しずつ高額になると、最後に積み上げた製造原価が想定よりも予算をオーバーしてしまうケースが考えられるからです。
日本国内の部品メーカー(中小規模)の価格競争力は航空先進国である米国や欧州と比較すると同等レベルでありつつも、設計・品質生産管理力は劣っています。それであれば、部品をわざわざ日本国内で製造する目的がありません。近年であれば、中国や台湾、更には東欧諸国の設計・品質生産管理力とコスト競争力が伸びている状況から、日本の部品メーカーとの差は開く一方です。事実、エアバスは東欧諸国、ボーイングは台湾やインドにおけるサプライチェーンを強化しています。
経済産業省はこの事実を把握しており、三菱スペースジェットの開発に合わせ、”クラスタ”と呼ばれる航空部品を生産する企業集合体を構築することを目指し、各地方自治体も旗振り役となり推進していました。しかし、三菱スペースジェットの開発中止により、このクラスタも解散になることも十分想定されます。
そのような状況で、日本国内で航空機を開発、生産するサプライチェーンを構築することは非常に困難な挑戦でした。
④プロジェクトを推進する中心人物が存在しなかったこと
プロジェクトには必ずプロジェクトマネジャー(PM)が存在します。このPMは責任と権限を持ち、何か問題があれば指揮を執りスケジュールに遅延が出ないよう対応します。今回の三菱スペースジェット開発においては、そのような性格を持つPMが不在であったことが各種報道にて取り上げられております。
日本人は以前より”指示待ち人間”と言われるケースが多々あり、細かく指示されたことは忠実にできる一方、トラブル発生時など臨機応変に対応することは苦手とされています。特に、予算の大きなプロジェクトや機体の新製品となると、万が一、失敗したときの自身の責任問題から委縮してしまうケースもあると感じます。
敗者に対してもの申すのは容易ですので、主観が多く入った記事となりました。製造業に携わる一員として、三菱スペースジェットの開発に携わっていた多くの人に敬意を表します。そして、この経験を基に、戦闘機や輸送機の開発、そしてエアバス・ボーイング向けコンポーネントの開発に活かせることを願っています。